Coarse grain defects are one of the common defects of aluminum alloy die forgings, which reduce the strength of forgings. In the coarse-grained structure in the forging and the transition zone from the coarse-grained structure to the fine-grained structure, the fatigue strength of the forged part is lowered. Henan Chalco Aluminum-Aluminum Alloy Forging mainly discusses measures to avoid and reduce coarse grain defects during the production of aluminum alloy die forgings.
1 coarse crystal appearance mechanism
After the metal is plastically deformed, the free energy is increased, the structure is in an unstable state, and when it is heated to a proper temperature, the crystal nucleus is re-formed and grown, and the microstructure composed of the new crystal grains is called recrystallization. Fine and uniform equiaxed grains are generally obtained after recrystallization, but if the heating temperature is favorable for grain growth or heating and holding time is too long, the recrystallized grains will grow into coarse grains]. Henan Chalco Aluminum-Aluminum Alloy Forging indicates that the process of grain growth can be divided into two types: one is gradually growing up, and the relative size between the crystal grains is basically close; the other is abnormal growth. The performance is that the relative size of each grain is extremely different, and some grains grow very coarse. In the coarse-grain defect waste of aluminum alloy die forgings, the probability of abnormal growth of recrystallized grains is large.
2 to avoid or reduce the coarse grain defects of the die forging
The coarse grain defects of the aluminum alloy die forgings are related to the material of the forging, the forging process parameters, the forging shape, the mold temperature, and the heat treatment process parameters.
2.1 Forging material
The aluminum alloy grades used to make die forgings are different, and the probability of coarse crystals in their products varies greatly. Forgings of aluminum-zinc-magnesium-copper alloys are less likely to have coarse crystal defects, while aluminum-copper-magnesium and aluminum-magnesium-silicon alloys have a relatively high probability of coarse grain defects.
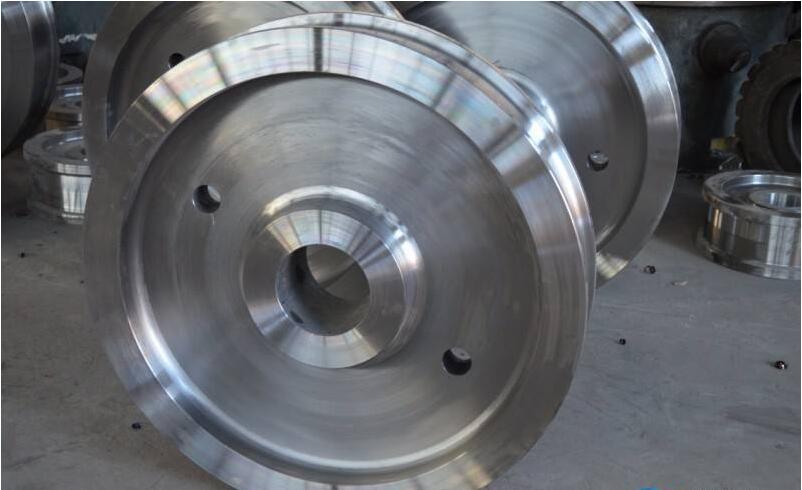
2.2 Forging process parameters and mold temperature
(1) Choose a reasonable final forging temperature
When the final forging temperature is too low, the forgings are prone to coarse crystals. Henan Chalco Aluminum-aluminum alloy forgings, especially aluminum-copper-magnesium and aluminum-magnesium-silicon alloys, must strictly control the final forging temperature, such as 2A11 (LY11). The final forging temperature of alloy blade die forgings must be higher than 390 °C, otherwise coarse crystals are easy to appear. Different forgings have different requirements on the final forging temperature, but all aluminum alloy die forgings require a final forging temperature of not less than 370 °C.
(2) The mold preheating temperature should not be too low
If the mold temperature is too low, the metal cooling rate in the cavity is accelerated, so that the deformation temperature of the metal is too low, making it difficult for the metal to fill the cavity and possibly forming a coarse crystal on the surface of the forging. The preheating temperature of the mold is related to the shape of the forging and the aluminum alloy grade. It is generally required to be controlled at 300 °C ~ 400 °C.
(3) The degree of deformation should not be too small
In particular, the degree of deformation of the last fire should not be too small. If the degree of deformation is small, the recrystallized nucleus is less, and the incubation period is long. After the die forging is heated (or heat treated) again, coarse grains will be formed. If the degree of deformation is as small as the critical deformation degree (about 3% to 15%), the recrystallized grains will grow sharply, causing coarse crystal defects in the forging. In the production, it is necessary to strictly control the die forging fire times of the die forgings and the amount of each fire pressing, to avoid the forgings being in a critical deformation state due to excessive die forging times and a small amount of pressing. Minimize the number of die forgings while ensuring that the metal can eventually fill the mold cavity and low current line requirements.
(4) The gross margin should not be too large
Henan Chalco Aluminum-Aluminum Alloy Forging means that especially for forgings with high ribs, if there is still excess metal after the metal has filled the cavity, if the upper and lower molds continue to move together, the excess metal at the web will follow the root of the rib. Direct flow into the burr groove in the nearest route may cause local coarse crystals to appear due to excessive deformation.
1 coarse crystal appearance mechanism
After the metal is plastically deformed, the free energy is increased, the structure is in an unstable state, and when it is heated to a proper temperature, the crystal nucleus is re-formed and grown, and the microstructure composed of the new crystal grains is called recrystallization. Fine and uniform equiaxed grains are generally obtained after recrystallization, but if the heating temperature is favorable for grain growth or heating and holding time is too long, the recrystallized grains will grow into coarse grains]. Henan Chalco Aluminum-Aluminum Alloy Forging indicates that the process of grain growth can be divided into two types: one is gradually growing up, and the relative size between the crystal grains is basically close; the other is abnormal growth. The performance is that the relative size of each grain is extremely different, and some grains grow very coarse. In the coarse-grain defect waste of aluminum alloy die forgings, the probability of abnormal growth of recrystallized grains is large.
2 to avoid or reduce the coarse grain defects of the die forging
The coarse grain defects of the aluminum alloy die forgings are related to the material of the forging, the forging process parameters, the forging shape, the mold temperature, and the heat treatment process parameters.
2.1 Forging material
The aluminum alloy grades used to make die forgings are different, and the probability of coarse crystals in their products varies greatly. Forgings of aluminum-zinc-magnesium-copper alloys are less likely to have coarse crystal defects, while aluminum-copper-magnesium and aluminum-magnesium-silicon alloys have a relatively high probability of coarse grain defects.
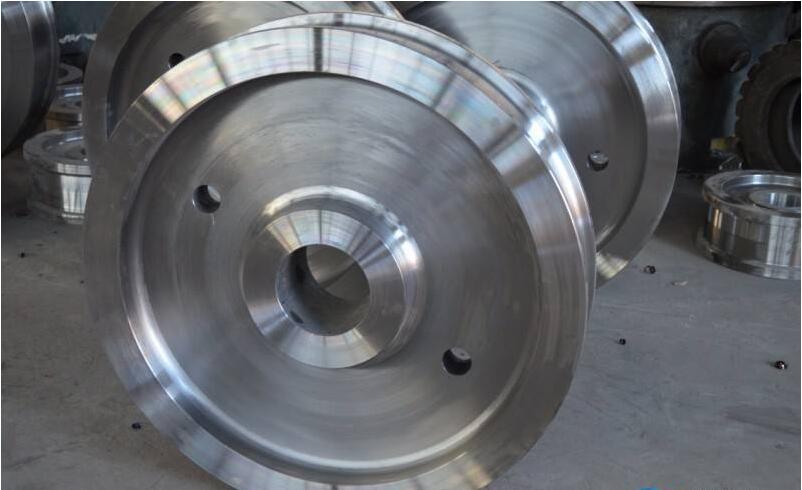
2.2 Forging process parameters and mold temperature
(1) Choose a reasonable final forging temperature
When the final forging temperature is too low, the forgings are prone to coarse crystals. Henan Chalco Aluminum-aluminum alloy forgings, especially aluminum-copper-magnesium and aluminum-magnesium-silicon alloys, must strictly control the final forging temperature, such as 2A11 (LY11). The final forging temperature of alloy blade die forgings must be higher than 390 °C, otherwise coarse crystals are easy to appear. Different forgings have different requirements on the final forging temperature, but all aluminum alloy die forgings require a final forging temperature of not less than 370 °C.
(2) The mold preheating temperature should not be too low
If the mold temperature is too low, the metal cooling rate in the cavity is accelerated, so that the deformation temperature of the metal is too low, making it difficult for the metal to fill the cavity and possibly forming a coarse crystal on the surface of the forging. The preheating temperature of the mold is related to the shape of the forging and the aluminum alloy grade. It is generally required to be controlled at 300 °C ~ 400 °C.
(3) The degree of deformation should not be too small
In particular, the degree of deformation of the last fire should not be too small. If the degree of deformation is small, the recrystallized nucleus is less, and the incubation period is long. After the die forging is heated (or heat treated) again, coarse grains will be formed. If the degree of deformation is as small as the critical deformation degree (about 3% to 15%), the recrystallized grains will grow sharply, causing coarse crystal defects in the forging. In the production, it is necessary to strictly control the die forging fire times of the die forgings and the amount of each fire pressing, to avoid the forgings being in a critical deformation state due to excessive die forging times and a small amount of pressing. Minimize the number of die forgings while ensuring that the metal can eventually fill the mold cavity and low current line requirements.
(4) The gross margin should not be too large
Henan Chalco Aluminum-Aluminum Alloy Forging means that especially for forgings with high ribs, if there is still excess metal after the metal has filled the cavity, if the upper and lower molds continue to move together, the excess metal at the web will follow the root of the rib. Direct flow into the burr groove in the nearest route may cause local coarse crystals to appear due to excessive deformation.