Forged aluminum radiator introduction
Forged aluminum radiator, unlike traditional iron forging, heat the aluminum to soften but do not liquefy, and then use high pressure to fill the mold cavity with aluminum. Usually we use this method to make a column fin, or the fin is a flow-optimized shape. The processing technology is complicated, the mold cost is high, and the shape of a single fin can be used as a runner design. AL6063/pure aluminum/AL2000 can be used. Among them, AL6063 and pure aluminum have better thermal conductivity than die-casting materials, and AL2000 has good strength requirements. At present, such processing technology is only applied in the industrial field.
Forged aluminum radiator features
The process of forged aluminum radiator is to heat the aluminum block to heat the aluminum block to the falling point and fill it with high pressure. The advantage is that the fin height can reach 50mm or more and the thickness is less than 1mm, which can be in the same volume. The maximum heat dissipation area is obtained, and the Forged aluminum radiator is easy to obtain good dimensional accuracy and surface finish. However, when forging, there is a necking phenomenon due to the cooling plastic rheology, which makes the heat sink easy to be thick and uneven, which affects the heat dissipation efficiency. Because of the low plasticity of the metal, cracking is likely to occur during deformation, and the deformation resistance is large. Forging machines that require large tonnage (more than 500 tons) are also costly due to the high cost of equipment and molds. And because of the high cost of equipment and molds, unless the mass production, the cost is too high.
There are not many manufacturers around the world that have the ability to manufacture Forged aluminum radiator. The most famous one is Japan's ALPHA, and Taiwan is Taisol, MALICO-Taiye Technology. The advantage of cold forging is that it can produce a Forged aluminum radiator with a heat dissipation area larger than that of aluminum extrusion, and because the aluminum extrusion process is stretching, the aluminum metal structure is expanded horizontally, and the cold satin direction is vertically compressed. Therefore, for heat dissipation, cold forging has a large advantage, and the disadvantage is that the cost is high, and there are not many manufacturers that can manufacture and manufacture technology.
Forged aluminum radiator, unlike traditional iron forging, heat the aluminum to soften but do not liquefy, and then use high pressure to fill the mold cavity with aluminum. Usually we use this method to make a column fin, or the fin is a flow-optimized shape. The processing technology is complicated, the mold cost is high, and the shape of a single fin can be used as a runner design. AL6063/pure aluminum/AL2000 can be used. Among them, AL6063 and pure aluminum have better thermal conductivity than die-casting materials, and AL2000 has good strength requirements. At present, such processing technology is only applied in the industrial field.
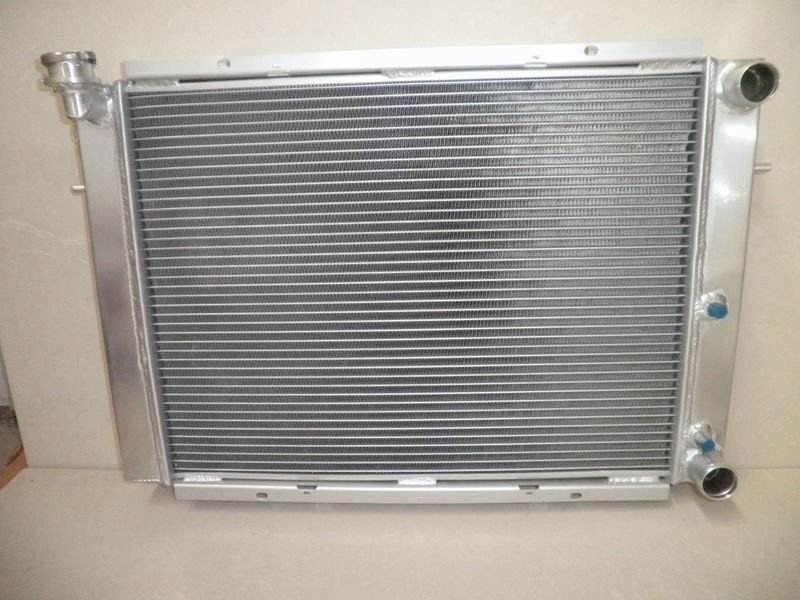
Forged aluminum radiator features
The process of forged aluminum radiator is to heat the aluminum block to heat the aluminum block to the falling point and fill it with high pressure. The advantage is that the fin height can reach 50mm or more and the thickness is less than 1mm, which can be in the same volume. The maximum heat dissipation area is obtained, and the Forged aluminum radiator is easy to obtain good dimensional accuracy and surface finish. However, when forging, there is a necking phenomenon due to the cooling plastic rheology, which makes the heat sink easy to be thick and uneven, which affects the heat dissipation efficiency. Because of the low plasticity of the metal, cracking is likely to occur during deformation, and the deformation resistance is large. Forging machines that require large tonnage (more than 500 tons) are also costly due to the high cost of equipment and molds. And because of the high cost of equipment and molds, unless the mass production, the cost is too high.
There are not many manufacturers around the world that have the ability to manufacture Forged aluminum radiator. The most famous one is Japan's ALPHA, and Taiwan is Taisol, MALICO-Taiye Technology. The advantage of cold forging is that it can produce a Forged aluminum radiator with a heat dissipation area larger than that of aluminum extrusion, and because the aluminum extrusion process is stretching, the aluminum metal structure is expanded horizontally, and the cold satin direction is vertically compressed. Therefore, for heat dissipation, cold forging has a large advantage, and the disadvantage is that the cost is high, and there are not many manufacturers that can manufacture and manufacture technology.